Las empresas expuestas a la escasez por la pandemia y a los cuellos de botella en el transporte marítimo se están viendo obligadas a replantearse sus operaciones.

Heineken vende 300 marcas a clientes de 190 países. Pero parte de la estrategia de la cervecera ha sido producir marcas regionales localmente y luego exportarlas a mercados más grandes. Cuando compró el control mayoritario de Red Stripe en 2015, repatrió la producción a Jamaica. Del mismo modo, la marca Dos Equis se fabricaba exclusivamente en México, aunque gran parte de sus ventas se realizaban en Estados Unidos y otros países.
Ese abastecimiento único se volvió en contra el año pasado cuando el gobierno mexicano declaró la cerveza no esencial y cerró temporalmente las cervecerías del país durante la primera ola de la pandemia. En lugar de renunciar a Dos Equis, Heineken se reagrupó, envió las etiquetas y botellas a los Países Bajos y comenzó a fabricar la cerveza allí. La producción en México se ha reanudado desde entonces, pero la empresa es ahora mucho más consciente de que necesita contar con centros de producción alternativos -con acceso a los suministros necesarios- para sus marcas más grandes y lucrativas.
En todo el mundo, las empresas se han encontrado con problemas en sus cadenas de suministro durante la pandemia y los cuellos de botella en el transporte que han seguido a la reanudación de las economías. Las líneas de producción de automóviles se han detenido por falta de semiconductores, los destiladores de licores se han quedado sin botellas y los grandes centros comerciales no tienen suficiente stock para la Navidad.
Estos problemas están obligando a replantear la estrategia empresarial. Durante décadas, las empresas daban prioridad a los costos por encima de todo cuando seleccionaban proveedores, construían fábricas y decidían la cantidad de existencias que debían mantener. Esta filosofía se denominaba generalmente “just in time” (justo a tiempo) porque hacía énfasis en mantener el inventario al mínimo y utilizar contratos flexibles a corto plazo que pudieran ajustarse rápidamente a los cambios en la demanda.
Pero la búsqueda de la eficiencia fue mucho más que eso. Las empresas también trasladaron la producción a lugares con salarios bajos, consolidaron los pedidos para maximizar las economías de escala y trataron de minimizar su presencia física en jurisdicciones con altos impuestos.
“Muchos de los modelos operativos de las cadenas de suministro que hoy vemos rotas, se cimentaron hace 20 años en lo que en aquel momento eran verdades universales, que buscar proveedores de bajo costo… tenía mucho sentido”, dice Brian Higgins, jefe de la práctica de operaciones y cadena de suministro de KPMG en Estados Unidos. “Se presta a estas largas cadenas de suministro porque se centran en el costo, no en el riesgo. Hemos visto esa fractura muchas, muchas veces”.
Las empresas no están abandonando del todo las políticas de la cadena de suministro existentes, pero las están renovando para crear una resiliencia adicional.
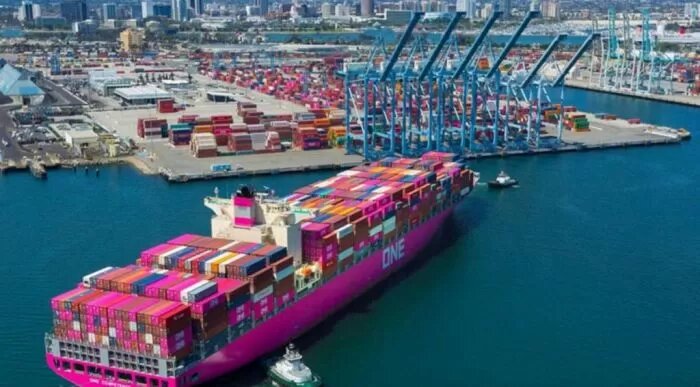
Algunas empresas están aumentando el inventario que tienen a mano y estableciendo contratos a más largo plazo con proveedores clave. Otras están diversificando su fabricación para crear centros regionales con proveedores locales e invirtiendo en tecnología para avisar con mayor antelación de posibles cuellos de botella. Algunas empresas también están investigando formas de trabajar con sus rivales para compartir información y desarrollar instalaciones de reserva de emergencia sin caer en la trampa de los reguladores de la competencia.
“Lo que les gusta a las empresas es optimizar el capital circulante. Por eso, muchos fabricantes recurrieron al inventario justo a tiempo y, antes de la pandemia, eso funcionó bastante bien”, dijo Carol Tomé, directora ejecutiva de UPS, en un reciente evento del sector.
“Pero cuando la pandemia llegó y todo se cerró, incluida la fabricación, y luego la economía empezó a abrirse y la demanda… se disparó, bueno, ese inventario justo a tiempo ya no funcionó. Ahora las empresas piensan que necesitan un inventario “por si acaso””, añadió.
LA PANDEMIA LO CAMBIÓ TODO
Los cambios están impulsados por la pandemia y la crisis de la cadena de suministro que le siguió. Pero también reflejan las tensiones geopolíticas entre China y Occidente y la creciente presión sobre las empresas para que reduzcan su huella de carbono.
Decenas de miles de pequeños cambios están reconfigurando fundamentalmente la forma en que se diseñan, fabrican y venden las cosas. En algunos casos, estos cambios están aumentando los costos y contribuyendo a la inflación, pero el resultado final puede ser un suministro más fiable y local, reduciendo tanto la volatilidad de los precios como las futuras emisiones de carbono.
Esta nueva mentalidad se arraigó en los primeros días de la pandemia, cuando una encuesta de McKinsey entre altos ejecutivos de la cadena de suministro descubrió que el 73% de las empresas había encontrado problemas con su huella de proveedores -desde escasez de piezas hasta retrasos en los envíos- que requerían cambios.
“La cadena de suministro es como tu auto. Si funciona, no le das importancia. Pero cuando se rompe, sí que se nota la diferencia”, dijo Hamid Moghadam, presidente de Prologis, un fondo de inversión inmobiliaria que invierte en instalaciones logísticas, en el mismo evento del sector. “La pandemia lo cambió todo“.
Un gran grupo industrial alemán sorprendido por la escasez de semiconductores ha pasado de acuerdos no vinculantes de tres meses con los proveedores a compromisos de 24 meses que le obligan a pagar por adelantado antes de recibir sus chips. “Teníamos que dar más estabilidad a la cadena de suministro”, dice un alto ejecutivo. “Es un cambio de un mercado de compradores a uno de vendedores”.
No es la única. Las automotrices estadounidenses Ford y GM están estableciendo asociaciones, en lugar de simples contratos con proveedores, con fabricantes de semiconductores para mejorar su acceso a los chips. Su rival alemán, Volkswagen, está estudiando la posibilidad de ampliar la duración de sus contratos con proveedores clave, y los grupos energéticos chinos se están apurando a firmar contratos de gas natural licuado de hasta 20 años, más del doble de la antigua duración normal. Una encuesta de seguimiento de McKinsey realizada este año reveló que el 61% de las empresas había aumentado el inventario de productos críticos y el 55% había tomado medidas para asegurarse de tener al menos dos fuentes de materias primas.
Como resultado, los costos de almacenamiento están aumentando considerablemente en muchos mercados, ya que los fabricantes y los minoristas aumentan los niveles de inventario. Las tasas de desocupación industrial en Estados Unidos -una medida del espacio de almacenamiento disponible- alcanzaron un mínimo histórico del 3,6% a nivel nacional en el tercer trimestre, según CBRE. En el Inland Empire de California, un cuello de botella clave cerca de los puertos de Los Angeles, las tasas de desocupación rozaron el 0,7%. Y el agente inmobiliario Cushman & Wakefield predice que el Reino Unido podría quedarse sin espacio para almacenes dentro de un año.
Con cadenas de suministro cada vez más complejas y catástrofes naturales que las interrumpen con mayor frecuencia, “hay que reinventar el ‘justo a tiempo'”, afirma Oscar de Bok, que dirige el negocio de la cadena de suministro de DHL. “Ya no se puede planificar de forma tan ajustada como se quería en el pasado”.
CADENAS DE SUMINISTRO “LOCALES POR LOCALES”
Abandonar el mantra de la “eficiencia por encima de todo” va más allá de los depósitos y los libros de pedidos.
Las empresas que habían consolidado su producción en uno o unos pocos lugares de bajo costo recibieron un duro golpe el año pasado, ya que los cierres relacionados con la pandemia y los cuellos de botella en los envíos las dejaron sin piezas clave o incluso sin mercancía para vender. El mensaje se vio reforzado por la inesperada helada de febrero en Texas, que cerró las plantas petroquímicas y provocó una escasez de resina, un ingrediente fundamental en todo tipo de productos, desde pajitas de plástico hasta piezas de autos.
La pandemia reforzó la posición de ejecutivos corporativos, que ya estaban estudiando la posibilidad de establecer redes regionales por otras razones, como eludir las crecientes tensiones entre Estados Unidos y China o aprovechar los incentivos gubernamentales destinados a estimular la fabricación local.
Las empresas multinacionales hablan ahora de cadenas de suministro “locales por locales”. Esto se debe, en parte, a que los problemas logísticos han acabado con las ventajas de enviar productos desde fábricas de bajo costo a medio mundo de distancia. Ahora se tarda entre 28 y 52 días en transportar un par de zapatos producidos en China desde Shanghai a Los Ángeles, frente a los 17 y 28 días que se tardaba antes de la pandemia. Y el costo total ha aumentado en u$s 1,77 por par, según un estudio de la consultora AlixPartners, un costo adicional que los miembros más pequeños de la industria, con márgenes de beneficio más estrechos, tendrán dificultades para absorber.
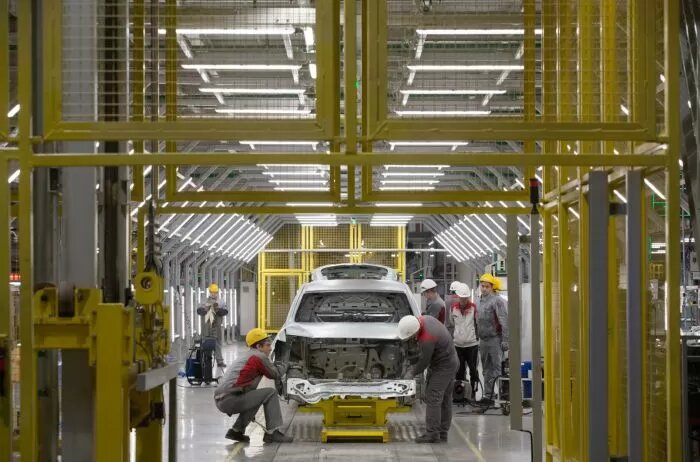
“El problema es la volatilidad. Si siempre hay un retraso de 10 días, se puede poner 10 días más de material en la cadena de suministro. Pero algunas cosas llegan a tiempo y otras se retrasan 20 días”, dice Volker Blume, responsable de control de materiales, transporte y garantía de entrega en el fabricante de automóviles alemán BMW. “Nuestros sistemas están diseñados para que los flujos sean fluidos”.
Los fabricantes y minoristas de todo tipo de productos, desde coches y calzado hasta vacunas, están redescubriendo las ventajas de tener proveedores más cerca de los consumidores. En sectores de importancia estratégica, como Salud, también están recibiendo apoyo gubernamental. Esto está reavivando el interés por la fabricación en Norteamérica, donde, por ejemplo, Ford y la surcoreana SK Innovation anunciaron recientemente un plan para construir una planta de baterías de iones de litio de u$s 5800 millones en Kentucky, y en Europa continental, donde Intel ha prometido invertir u$s 20.000 millones en la fabricación de semiconductores.
“El péndulo ha oscilado y… no creo que vuelva atrás del todo. Ni siquiera China va a ser el centro de fabricación de bajo costo que [una vez] fue”, dice Simon Freakley, director ejecutivo de AlixPartners. “Esto significa que zonas como Texas y Kentucky se vuelven [más atractivas porque] tienen la ventaja añadida de estar justo a tiempo y por si acaso”.
Resilience, una empresa biofarmacéutica con sede en San Diego, es una de las beneficiarias de esta tendencia. Fundada durante la pandemia, está especializada en la fabricación de alta tecnología en tierra. Recibió una inversión directa del gobierno canadiense por u$s 164 millones para su planta de Ontario y ha conseguido contratos de Moderna y otras empresas que han desarrollado vacunas y medicamentos para producirlos en Norteamérica. Ya tiene cuatro centros en funcionamiento y planea construir al menos otros seis.
“Es un mito que el costo dependa de la geografía“, dice el cofundador y director ejecutivo de Resilience, Rahul Singhvi, que anteriormente trabajó para Takeda, el grupo farmacéutico japonés. “Teníamos tecnologías de fabricación que podíamos desplegar para reducir el costo incluso en Japón. Era más barato que algunos mercados indios y chinos”.
RESPONSABILIDAD COMPARTIDA, RIESGO COMPARTIDO
VW y BMW han intentado estandarizar los componentes de sus distintos modelos y marcas para que los proveedores tengan volumen suficiente para fabricar a nivel regional.
La plataforma de diseño de VW para los autos a nafta y diésel “es muy flexible, de modo que si el volumen disminuye podemos combinar los autos con motor de combustión de diferentes marcas en una planta y rediseñar los demás”, dice Arno Antlitz, director financiero de la empresa. “Estamos reduciendo mucho la complejidad porque tenemos que hacerlo“.
Aunque gran parte de la atención prestada a la localización ha sido impulsada por cuestiones logísticas, los ejecutivos dicen que la tendencia también encaja con sus esfuerzos para abordar el calentamiento global, y capitalizar los cambios en las políticas gubernamentales.
Reducir el número de piezas y productos que se envían por todo el mundo es una forma sencilla de mejorar la huella de carbono de una empresa. Algunos grupos también están trasladando su fabricación a lugares en los que abunda la energía renovable y hay mercados importantes para sus productos, como la provincia china de Yunnan, donde la energía hidroeléctrica la ha convertido en un centro de producción de aluminio.
Al mismo tiempo, los incentivos financieros para la ubicación de las plantas están cambiando. No sólo los gobiernos se esfuerzan por impulsar la fabricación nacional, sino que algunas de las ventajas de la producción en jurisdicciones de baja tributación se están reduciendo.
El innovador acuerdo mundial sobre el impuesto corporativo, firmado en octubre, exige que las empresas paguen al menos una tasa efectiva del 15% y declaren sus ganancias. Y que paguen más impuestos en los países donde hacen negocios. Esto eliminaría los incentivos actuales para que las empresas eviten tener una presencia física en los países de alta tributación donde tienen muchas ventas, de modo que puedan trasladar los ingresos y beneficios a otros lugares, dice Kate Barton, de EY.
Los ajustes en las cadenas de suministro van más allá de los cambios físicos. Muchas empresas están utilizando la tecnología para identificar rápidamente los retrasos en la cadena de suministro. BMW ha aumentado el uso de rastreadores digitales para seguir sus piezas por toda Europa y recibir alertas en tiempo real si un camión se retrasa. La actual demora en puertos clave significa que los tiempos de transporte marítimo son más variables, por lo que el fabricante de automóviles está trabajando con un par de startups que están tratando de desarrollar algoritmos de predicción. Pero la información de los proveedores directos sólo puede llegar hasta cierto punto.
“Si tenés buena información sobre tu cadena de suministro, necesitás menos existencias y puedes disminuir los topes”, dice Blume, de BMW. “Necesitás una solución de comunicación estandarizada que permita a los participantes en la cadena de suministro mirar con más detalle”.
Por eso, las principales automotrices alemanas y sus mayores proveedores –Bosch, Siemens y Schaeffler, entre otros- se unieron la primavera pasada para fundar Catena-X. Esta alianza automovilística establece normas para el intercambio de información y datos, con el fin de facilitar a todos ellos el conocimiento de lo que ocurre no sólo en sus proveedores directos, sino también en los cientos de miles de empresas más pequeñas de las que dependen.
Al mismo tiempo, los minoristas y los fabricantes que pertenecen al Foro de Bienes de Consumo están estudiando la forma de colaborar para aumentar la resiliencia, tal vez invirtiendo en instalaciones de reserva compartidas que serían necesarias en una situación de emergencia. Esto podría incluir puertos alternativos, depósitos adicionales y camiones. Es probable que esto requiera aprobación regulatoria debido a los riesgos de cárteles, pero hay precedentes. El gobierno del Reino Unido le permitió a las tiendas de comestibles y a los proeedores trabajar juntos para desviar los suministros de los restaurantes a los supermercados en los primeros días de la pandemia.
Las conversaciones están en una fase inicial, pero “el hecho de que la palabra ‘colaboración’ forme parte incluso de una reunión de la junta directiva es un cambio”, afirma Ruediger Hagedorn, director de la cadena de valor integral del grupo. “Si tienes instalaciones compartidas, compartes el riesgo”.
Acumular stock es mucho más fácil que trasladar fábricas o acordar compartir espacio con un competidor, y no está nada claro que las empresas vayan a cumplirlo. Mientras que el año pasado el 93% de las empresas dijeron a McKinsey que tenían la intención de hacer que su cadena de suministro fuera más flexible, ágil y resistente, sólo el 15% había realizado cambios estructurales cuando llegó la encuesta de este año.
Sin embargo, Daniel Swan, que dirige la práctica de operaciones de la consultora, afirma que “hay un aumento significativo del compromiso de los directores generales con los temas de la cadena de suministro. Eso me anima a pensar que no será un destello”.
Por El Cronista.